
Operations Analytics
Businesses seeking major in-roads in resource allocation, workflow improvements and risk management cannot overlook the potentials analytics presents. The headache to balance cost, speed, and quality is a hand full. Above and beyond, flexibility and dependability are still important considerations. Our operational analytics models will help managers to navigate through the tough decisions they often make. Below are a few to be explore:
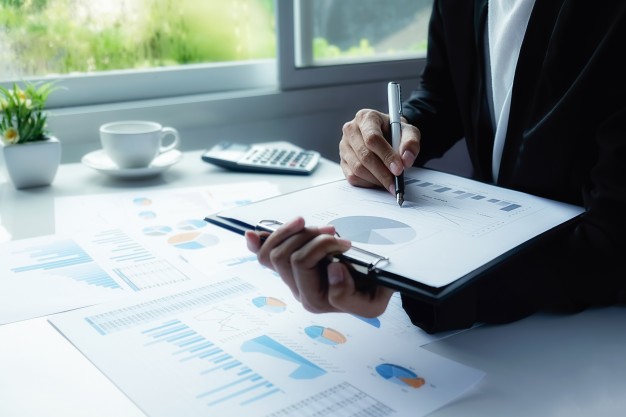
Manage material supplies, employee production timelines, storage capacities and retail engagements in line with seasonal demands.
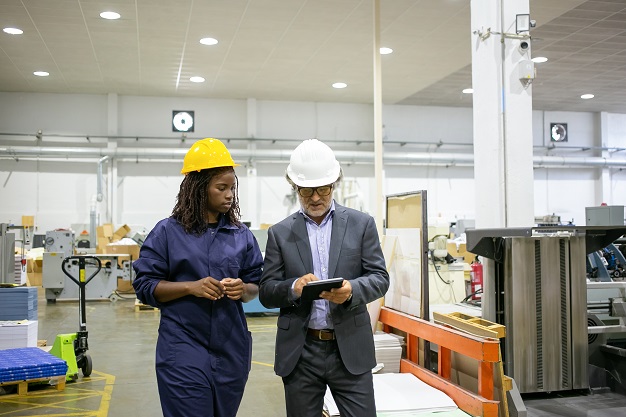
Productivity is higher when workflows are efficient; improving gross margins contrary to passing cost inefficiencies to clients through pricing.
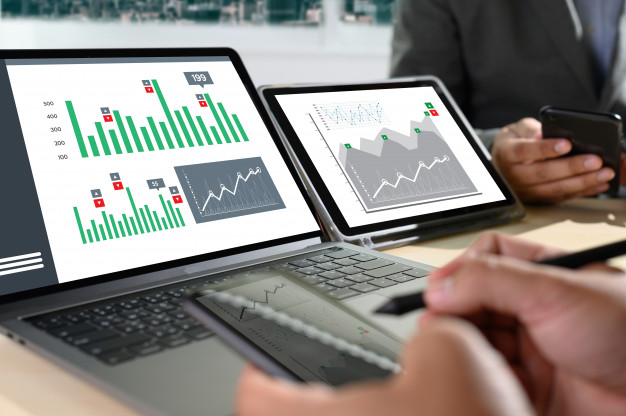
Develop early warning signals to detect and fix workflow wastes and policy deviations that open up potential fraud issues.
Demand And Resource Allocation
As marketing creates demand, operations takes feedback to procure resources in time to increase throughput efficiency and lower costs. Operational analytics will predict the outcome of marketing efforts and prompt managers to schedule material, labour and machine capacities needed to achieve target results.
Operations managers will reflect on geographic demand variations to comprehend demographic, seasonal and cultural issues that will facilitate resource schedules, capacity planning, quality control and maintenance arrangements. This will minimize holding costs, reduce freight charges and enable them obtain the right quantity discounts.
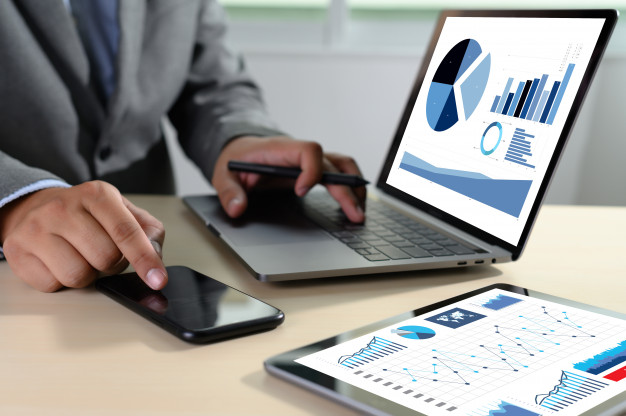
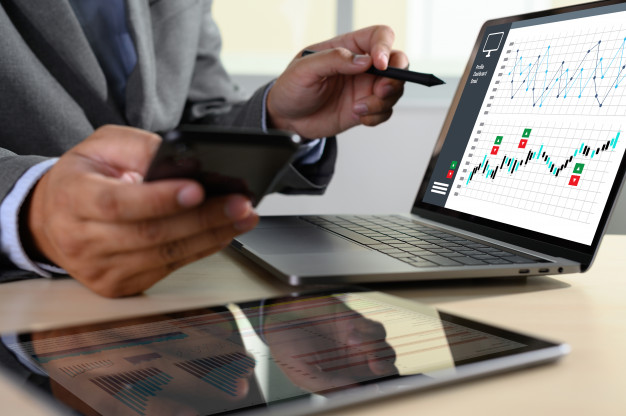
Workflow Analysis & Management
Workflows are repeatable set of actions in service delivery or goods production. They may be internally-held or outsourced; some being value adding, others identifiable as non-value adding by monitoring key performance activities (KPA). Actual workflow times will be randomly clocked and tested against their acceptable mean in six-sigma analysis.
Our solutions can predict expected resource utilization rates to optimize scheduled outcomes. Though short-term sales surges engages capacity buffers, where failings are anticipated, they can be addressed to improve customer equity.
Simulations to predict the likelihood of equipment breakdowns by studying past events improves considerations on maintenance schedules. Part replacements, set-ups and flexibility adjustments will ensure a smooth running workflow process.
Quality, Risks And Compliance
Defects costs more to correct. Firms invest in systems to help them get it right at their first attempt. Toyota among other institutions get insight into supplier operations through interconnected systems to evaluate the impact of decision changes. Supplier relations are managed over the long-term with feedback to maintain quality standards.
Consistency, reliability, flexibility and durability are some of the quality considerations that attract customers. Brand damages are avoidable when analytics facilitates quality control by detecting errors, policy breaches and defects. Root cause analysis are quickly researched to promote innovative practices during quality training sessions.
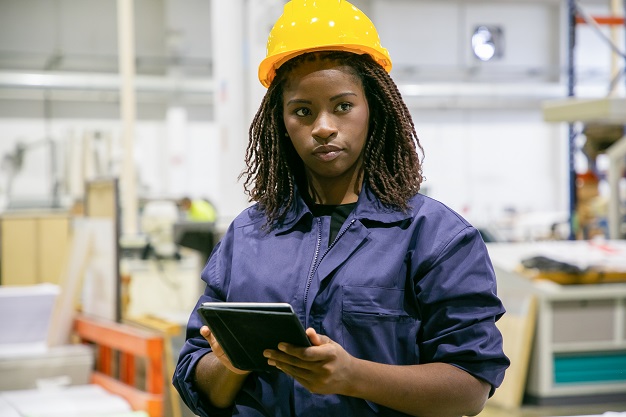
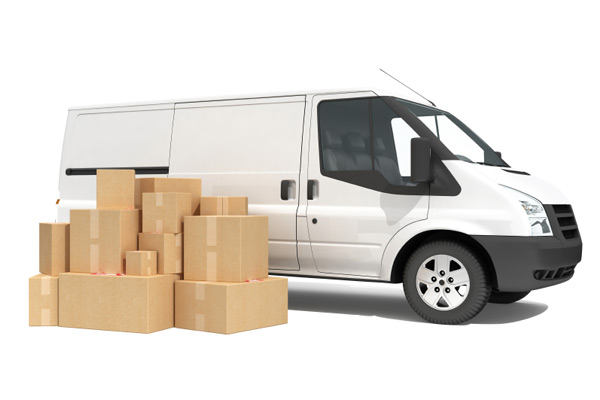
Warehouse & Routing Analysis
Resources are gathered from various locations to satisfy customer needs at other locations. A geographic analysis of movements to satisfy the needs of client segments with the associated cost can best be described as routing analysis. This establishes the route channels and frequency of use that best achieves the service delivery objectives.
The location of warehouse facilities, the size thereof and facility layout are essential elements that impact waiting times, material handling and holding costs. Besides, changes in market demand will require modifications to established norms so investments are made to acquire new equipment or expand existing facilities.
The operational analytics models are tailored to enable users derive cost management and make them competitive in their operating environment.